こんにちは、かじつとむです。
品質管理において最も大切なことは、不良を市場に出さないことです。
不良を市場にださないためには、商品を検査することで不良であるかどうかを確認し、手直しか廃棄する必要があります。
しかし、実際どのような検査をすることで不良を出さないようにしているのでしょうか?
今回は、検査についてと商品が顧客にわたるまでの検査の役割について説明します。
この記事を読むことで以下のことがわかります。
- 検査について理解することができる
- 役割別の検査の種類について理解することができる
それでは、いってみましょう!
工場の検査とは
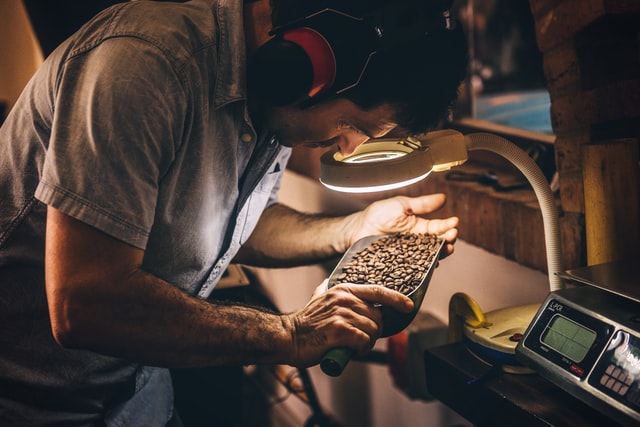
検査とはなんでしょうか?辞書で調べると以下の意味になります。
ある基準をもとに、異状の有無、適不適などを調べること
Weblio:https://www.weblio.jp/content/%E6%A4%9C%E6%9F%BB
このような意味から工場や製造業における検査とは、設計品質を示した仕様書や図面と比べて、実際につくられた商品が異常であるかどうか調べることになります。
設計品質は、顧客やが満足する性能・機能・デザイン等を決めている品質となります。
よって設計品質と比べて、実際の商品が違っていたら不良ということになります。
検査の仕事は主に3つあります。
- 設計品質にしたがって、商品の合否判定を行い、不良を除去する
- 商品の検査結果を記録する
- 商品の検査記録から、前工程にフィードバックすることで不良防止に役立てる
検査の最優先の仕事は、設計品質にしたがって、商品の合否判定を行い、不良を除去することです。
これをやらなければ不良が顧客に渡ってしまい、迷惑をかけたり会社の信用を失ってしまうからです。
よって、まずは商品の合否判定を行い、必ず不良を除去することが一番重要です。
検査の他の仕事は商品の検査結果を記録することです。
これは、検査した合否の結果だけではなく、なぜ合格なのか不合格なのかを記録することです。
たとえば、図面の寸法が〇〇±△△mmとなっていた場合、合否結果と実際に測定した数値を記録することです。
なぜ記録する必要があるのでしょうか?
答えは不良が発生した場合、不良の兆候を見定めることで未然防止が可能になるからです。
たとえば、先ほどの図面の寸が〇〇±△△mmに対して記録をとっていたとしましょう。
その記録を時系列で並べたときに、だんだんと寸法が短くなる傾向があるとすれば、経年によって寸法が短くなっている可能性が考えられます。
つまり、設備の劣化によって寸法が短くなった可能性を考えることができ、その対策を行うことができます。
このように、検査結果を記録することで不良が発生する兆候や原因を考える材料にもなります。
また、検査は先ほどの検査記録を使って、前の工程にフィードバックを行い不良防止に役立てることも仕事です。
では、実際にどのような検査が行われているのでしょうか?それを次に説明します。
役割別の検査の種類

実際に商品をつくる際には、検査を役割別に配置することで不良を除去しています。
役割別の検査方法について以下にまとめます。
- 受入れ検査
- 工程内検査
- 出荷検査
また、役割別の検査方法を時系列で表すと以下のようになります。
工場では、完成品を検査する出荷検査だけではなく、材料や購入部品を検査する受入れ検査と商品がつくられる途中の仕掛品を検査する工程内検査の3種類の検査を行っています。
なぜ、こんなにも検査を行う必要があるのでしょうか?
答えは、不良そのものをなくす防止を行うためです。
完成品のみの出荷検査だけ行っていると、不良が顧客にわたることは防げますが、どの工程や段階で不良が起きたのか特定ができません。
そのため、購入品自体に不良がないのかを検査する受入れ検査や工程ごとに不良が発生しているかを確認する工程内検査があります。
役割別の3つの検査について説明します。
役割別の検査の種類 その1:受入れ検査
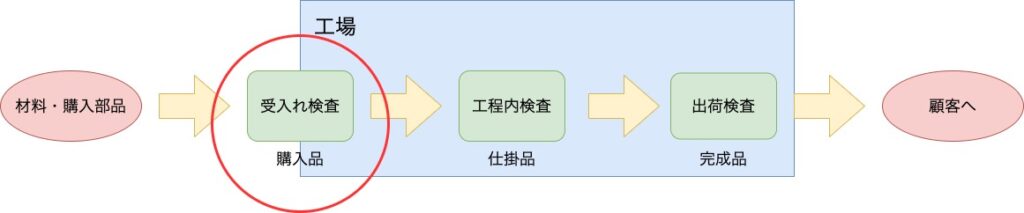
受入れ検査は、材料や購入部品を入手した際に行う検査です。
どんなに工場の能力が高くても材料や購入部品に不良があると、完成品が不良になってしまいます。
受入れ検査は、材料や購入部品の品質はもちろんのこと、発注数量と入手個数が同じであるかなんてことも確認します。
これらの品質や個数を購入仕様書で示されており、購入仕様書をもとに確認を行います。
役割別の検査の種類 その2:工程内検査
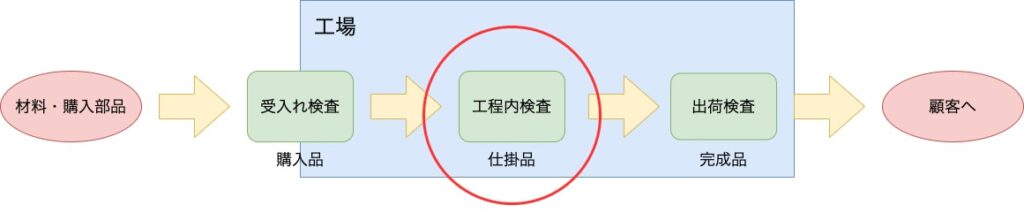
工程内検査は、商品が完成するまでの工程間で行う検査です。
各工程の間に決められた検査員を配置して行う検査と工程の作業者が自ら行う検査の2つがあります。
工程の作業者が自ら行う検査のことを自主検査といい、これは次の工程に不良を流さない考え方になります。
工程内検査で見つかる不良はすべて内部不良となります。
自分の工程内で不良を見つけることで、不良の原因を考え、不良の防止に役立てます。
このように、工程内検査は不良の防止を行うことで手直しや廃棄による労務費の削減を狙う検査ともいえます。
役割別の検査の種類 その3:出荷検査
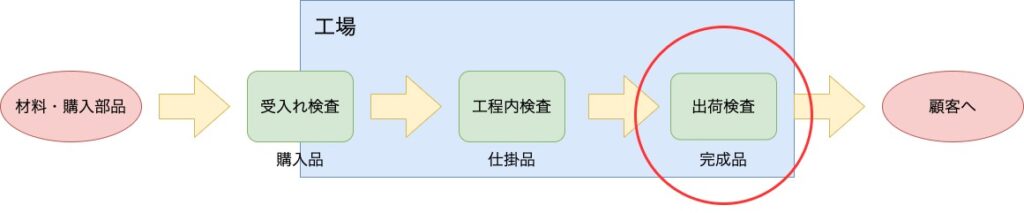
出荷検査は、完成品を顧客にわたす前に行う検査です。
ここでは、完成品が設計品質を満たすかどうか確認します。
また、出荷検査では輸送中に完成品が破損しないように、梱包状態も含めて確認します。
出荷検査の最大の目的は、不良品が顧客にわたらないことです。
ですのでより厳しい検査がここでは行われています。
不良を顧客に渡さない! 検査について:まとめ
いかがでしたでしょうか?以下まとめです。
- 検査とは、設計品質を示した仕様書や図面と比べて、実際につくられた商品が異状であるかどうか調べることである
- 検査は主に不良を除去すること、検査結果を記録すること、検査記録を前工程にフィードバックすることが仕事である
- 検査方法は、材料や購入部品を検査する受入れ検査、商品がつくられる途中を検査する工程内検査、完成品を検査する出荷検査の3つがある
検査1つとってもここまで考えなければならないなんて驚きですよね。
もし製造業に関わるのであれば、検査の意識を理解しながら、どうすれば不良を出さないようにするのかぜひ考えてみてください!
最後まで、この記事を読んでいただきありがとうございました!
検査などの品質管理についてもっと勉強したい方へ

検査等の品質管理についてもっとよく勉強したい方は「〈図解〉基本からよくわかる品質管理と品質改善のしくみ」という本がおすすめです。
この本では、今回紹介した検査といった品質管理や品質の基礎についてわかりやすくかつ網羅的に解説しております。
具体的には品質を守るための検査や予防について、データを数値化する方法、問題解決手法など、QC7つ道具についてといった品質管理に関わる内容を一通り理解できるような本となっております。
品質管理の仕事について知りたい方や、品質管理ってどういう仕事なのかわからない新入社員、品質管理の仕事を説明する中堅社員の方にもぜひおすすめの本となっております。
皆さんもぜひ品質管理について勉強し、どうすれば不良を出さないのか、品質を上げることができるのかぜひ考えてみましょう!
最後までこの記事を読んでいただきありがとうございます!
新しい学びを探したい方はUdemyがおすすめ!

コメント